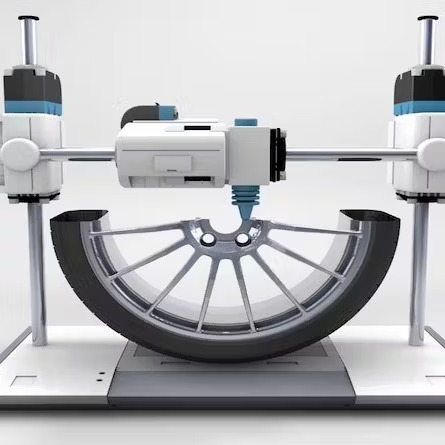
Honda may be a well-known brand within the world of automobiles and bikes, with a long-standing history of development and greatness. The Honda Hustling Group could be a department of the company that specializes in motorsports, with a focus on hustling bikes. As of late, the group has made features with its use of Metal 3D Printing Technology to form custom parts for their bikes. In this article, we are going investigate how the Honda Dashing Group is utilizing metal 3D printing innovation for their cruisers.
Contents
- 1 What is Metal 3D Printing Innovation?
- 2 How is the Honda Dashing Group Utilizing Metal 3D Printing Innovation?
- 3 What Are the Metal 3D Printing Materials?
- 4 Tungsten and Amalgams:
- 5 Is 3D Printed Metal Durable?
- 6 What Metal Powder Is Utilized for 3D Printing?
- 7 The Materials Metal 3D Printing Technology
- 8 Fabulous weldability Of Metal 3D Printing Technology
- 9 Key Applications:
- 10 Aviation
- 11 Common Electric
- 12 Therapeutic
- 13 Lima Corporate
- 14 Great inflexibility
- 15 How Is Metal Powder Used for Metal 3D Printing Technology?
- 16 Outline Of Metal 3D Printing Technology
- 17 Copyright and Trademark Takes note
- 18 Benefits of Metal 3D Printing Innovation for the Honda Dashing Group
- 19 Future of Metal 3D Printing Innovation for the Honda Dashing Group
- 20 Conclusion
What is Metal 3D Printing Innovation?
3D printing innovation has been around for a few decades, and it has made noteworthy strides in later a long time. Metal 3D Printing Technology may be a modern and energizing advancement within the world of added substance fabricating. It permits for the creation of complex metal parts that would be troublesome or outlandish to create with conventional fabricating strategies. This innovation works by dissolving metal powder and layering it to make a 3D protest.
Metal 3D printing is a laser-based technology that fuses metal particles layer-by-layer. This technology is commonly used for prototyping, production of parts with complex geometries, and end-use parts, as well as for the reduction of metal components in an assembly Metal 3D Printing Technology is supplied with a growing family of materials. This satisfies the needs of diverse industries from jewelry to aerospace, and medical to plastics manufacturing. Some processes and equipment are material-specific and limited in their range, while others are capable of using a range of materials.
How is the Honda Dashing Group Utilizing Metal 3D Printing Innovation?
The Honda Dashing Group is utilizing Metal 3D Printing Technology to form custom parts for their bikes. These parts are planned to be lightweight and durable, with a tall level of precision. The group employments this innovation to make parts such as brake calipers, footpegs, and exhaust frameworks.
One of the critical preferences of Metal 3D Printing Technology is that it permits for the creation of complex shapes and plans. The Honda Hustling Team takes full advantage of this include, making parts that are not only utilitarian but moreover stylishly satisfying. By utilizing this innovation, the group can make parts that are one of a kind to their bikes, giving them an edge in competition.
How Do I Select the Most excellent Type of Metal 3D Printing Technology?
Selecting the most excellent sort of 3D printing is complex. Underneath are valuable steps to go through when choosing which metal 3D printer forms to select:
Audit portion prerequisites. For illustration, grant thought to the layer determination, the require for the generation of fine detail, as well as the specified mechanical properties and corrective quality contemplations.
Select a fabric family for the part.
Once the material has been chosen, audit the accessible forms that utilize that fabric to consider the leading one to create the required comes about.
Check the accessibility of assets, counting providers for the fabric, time, and costs.
In choosing the finest sort of Metal 3D Printing Technology, it is critical to build experience—or get to great exhortation from those as of now commonplace with the different alternatives.
What Are the Metal 3D Printing Materials?
There’s a long and developing list of metal-type alternatives in Metal 3D Printing Technology materials. The foremost common metal sorts are:
Stainless Steel:
- By and large in 3 amalgam bunches: 304, 316, and 17-4. These are corrosion-resistant and of tall strength when not permeable.
- Instrument Steels D2, A2, and H13: Have tall quality, are hardenable, wear-resistant, and are appropriate for kicks the bucket and instruments.
- Titanium and Ti64: Materials that are perfect for lightweight parts and have tall quality.
- Aluminum 7075, 4047, 6061, 2319, 4043: These are different lightweight amalgams for common, lightweight components.
- Inconel® 718, 625: These have moo erosion and high-temperature resistance for purposes such as motor parts.
- Cobalt Chrome: Superalloy for biomedical and aviation applications.
- Gold/Silver: Unadulterated metals for jewelry and restricted biomedical employments.
- Niobium, Niobium-Zirconium: These are high-temperature and high–chemical–resistance combinations for aviation utilize.
- Tantalum: Comparable to Niobium but with better chemical resistance.
- Hastelloy® Nickel Chromium: Materials that are tough—temperature-resistant and crack-resistant. Commonly utilized for turbine and atomic components.
Tungsten and Amalgams:
Materials with super-high thickness. Utilized commonly for radiation shields, collimators, and motor parts.
When Did Metal 3D Printing Technology To begin with Show up?
The earliest commonsense execution of a Metal 3D Printing Technologyr was the EOSINT M250. It was propelled in 1994 by ElectroOptical Frameworks. It combined metal with a lower-temperature combination, which was intertwined to couple the primary particles. In 2004, EOS propelled the EOSINT M270. It was the primary PBF framework that utilized a diode pump 200W laser to soften the metal feedstock. Since at that point, there has been an exponential increase/improvement in strategies, materials, and resolutions.
Is 3D Printed Metal Durable?
No. Not all 3D printed metals are strong. Metal 3D Printing Technology forms offer focal points but endure drawbacks interesting to their characteristics and fabric limitations. However, by selecting the correct handle and materials to suit the application, surprising comes about can be accomplished.
What Metal Powder Is Utilized for 3D Printing?
Metal 3D Printing Technology powders come in a extend of sorts, materials, and grades. These shift from the moderately coarse powders required for DMLS (and related innovations) down to the reviewed nanoparticles utilized in fabric jetting. The powders too extend from circular particles to unpleasant shapes, depending on the nature of the method and the prerequisites within the conclusion item.
The Materials Metal 3D Printing Technology
Metals have been the fastest-growing portion of the 3D printing materials showcase since 2012.
Metal 3D Printing Technology forms utilize high-quality metal materials. They are regularly delivered in powder frame and must meet certain characteristics, like molecule shape and measure, and powder thickness.
Compared with conventional fabricating handle, the run of accessible 3D-printable metals remains constrained.
Usually due to the reality that particular materials adjusted or delivered for Metal 3D Printing Technology innovations can take a long time to create.
In any case, a few forms like DED can utilize metals initially created for conventional forms, for example, in wire frame.
As of now, the foremost commonly utilized materials for metal 3D printing incorporate lightweight metals like aluminum, titanium and stainless steel.
However, the utilize of hard-headed metals and cobalt chrome combinations is additionally expanding, largely driven by applications within the aviation and oil & gas businesses.
Within the table underneath, we’ve distinguished the more common Metal 3D Printing Technology and their normal applications.
Fabric Portrayal
Aluminum
(AlSi10Mg, AlSi12, AlSi12Mg combinations, Scalmalloy)
Lightweight fabric with great alloying properties
Tall erosion resistance
Simple post-processing (e.g. to machine, weld and clean)
Tall strength-to-weight proportion
Tall temperature resistance and warm and electrical conductivity
Key Application:
Aluminum can be utilized to create lightweight, geometrically complex parts and is especially utilized within the car and aerospace industries.
Titanium
Commercially immaculate (Review 1 and 2)
Titanium amalgam Ti6Al4V (Review 5)
Titanium amalgam Ti 6AL-4V ELI (Review 23)
Fabulous biocompatibility
Great quality and durability
Tall erosion resistance
Tall thickness
Key Application:
Titanium is in a perfect world suited to motorsport, flying and medical/dental applications.
Stainless steel
(17-4PH and 316L amalgams)
Tall hardness and sturdiness
Tall resistance to erosion
Great weldability
Tall ductility
A cheaper elective to titanium or nickel
Key Application:
Stainless steel has particularly found its check within the aviation, oil & gas, nourishment handling, and therapeutic businesses.
Cobalt chromium combination (CoCrMo)
Great quality
Tall erosion resistance
Temperature resistance
Non-magnetic
Biocompatible
Key Application:
Therapeutic (surgical inserts as counterfeit joints counting knee and hip joints) and dental. The metal has moreover been utilized to deliver parts for gas and wind turbines, as well as motor components.
Nickel alloys (Inconel 625, Inconel 713, Inconel 718, Inconel 738, Hastelloy X)
Tall erosion resistance
Incredible quality and sturdiness at higher temperatures
Fabulous weldability Of Metal 3D Printing Technology
Key Applications:
Nickel amalgams are perfect for high-temperature applications inside the aviation, chemical process and control industry, as well as fly motor gas turbine edges.
Copper-based amalgams
Fabulous warm and electrical conduction
Aviation
The aviation industry has been a tremendous pioneer of Metal 3D Printing Technology . By utilizing the innovation, aviation companies trust to create more proficient, lightweight airplane parts to progress airplane execution.
Inside the aviation industry, metal 3D printing is utilized in a extend of applications, from useful models to tooling, substitution parts and auxiliary flying machine components.
Common Electric
A awesome illustration is Common Electric (GE), which is broadly utilizing Metal 3D Printing Technology to create and create modern items. GE’s auxiliary, GE Flying, is creating fuel spouts for the Jump family of fly motors, with an point to make 100,000 fuel spouts by 2020.
Having accomplished the point of reference of 30,000 3D-printed fuel spouts in October 2018, GE looks like it’s well on its way to satisfying this objective.
Utilizing progressed plan instruments and Electron Pillar Softening technology, GE’s engineers were able to make a fuel spout 25% lighter and 15% more fuel effective than its customarily delivered partner.
The breakthrough in this case is that the fuel spout was printed as a single unit, while past models joined 20 partitioned parts which required to be hence amassed.
But GE has not halted here. The company is additionally building its GE Catalyst, an progressed turboprop motor that has more than a third of its components 3D printed in different metals.
Comparative to its fuel spouts, the engineers behind the turboprop have accomplished significant portion combination, decreasing the number of parts created from 855 to fair 12. A overhaul will also offer assistance to decrease the fuel burn of an motor by as much as 20%.
Car
Automakers have been utilizing Metal 3D Printing Technology since the technology’s early days — Passage Engine Company, for case, strikingly bought the third 3D printer ever made.
For numerous a long time, metal 3D printing has demonstrated to be a cost-effective apparatus for prototyping and creating dances and installations. Be that as it may, headways with the innovation mean that more openings are opening up for end-part generation.
Car companies can use metal 3D printing to form lightweight metal parts, leading to enhanced vehicle execution and lower fuel utilization. This is often especially advantageous for the motorsports industry, where 3D-printed car parts can offer hustling groups noteworthy execution points of interest.
Another zone of intrigued for the industry is additionally using Metal 3D Printing Technology to create save parts that are regularly created in moo volumes. 3D printing save parts on demand empowers automakers to get parts at the point of require, diminishing stock costs and expanding dexterity.
BMW
BMW 3d printed roof bracket
BMW is another company utilizing Metal 3D Printing Technology extensively. Most outstandingly, the company has as of late moved into the arrangement generation of a 3D-printed metal component for its 2018 BMW i8 Roadster vehicle.
Utilizing topology advancement, creators were able to upgrade the vehicle’s roof bracket — a installation for the folding/unfolding component of the vehicle’s delicate best. 3D printed in aluminum combination powder (AlSi10Mg), the unused roof bracket is 44% lighter than its customarily made partner.
Furthermore, engineers enhanced the plan of the bracket to dispose of back structures. By doing so, the team was able to extend throughput from 51 to 238 of these parts per stage. This makes BMW’s roof bracket the to begin with car component to be mass-produced with the assistance of metal 3D printing.
Bugatti
An energizing application of metal Metal 3D Printing Technology comes from extravagance car manufacturer, Bugatti. The French automaker has created a 3D-printed brake caliper to be utilized on its Bugatti Chiron supercar.
An fundamental portion of the braking framework, the brake caliper has been made lighter and more grounded much obliged to 3D printing. Measuring 41 x 21 x 13.6 cm, the portion took 45 hours to print utilizing SLM technology and titanium powders.
By utilizing Metal 3D Printing Technology g, Bugatti moreover accomplished a 40% weight decrease for the caliper, when compared to machined aluminum elective.
In 2018, the company effectively tried the brake caliper, demonstrating that it can meet extraordinary quality, firmness and temperature necessities.
Audi
Audi presents a diverse trade case for metal 3D printing. In this case, the German automaker is using the innovation to deliver save parts that are in moo demand.
Metal 3D printing permits Audi to deliver these parts on request, creating and providing save parts as they are required. This in turn significantly disentangles coordinations and warehousing.
Audi recognized that littler, complex components would be most suited for metal 3D printing. A great case of a component is water connectors, which Audi is as of now creating for the Audi W12 motor. The company says that the stack capacity of the components is comparable to that of parts fabricated utilizing conventional strategies.
Therapeutic
Within the restorative field, metal 3D printing allows highly tweaked restorative gadgets, like orthopedic inserts, to be made.
It’s distant from unordinary for off-the-shelf orthopedic inserts to be utilized for substitution surgeries. Be that as it may, pre-assembled inserts can in some cases cause issues after the surgery as they do not continuously fit appropriately.
To dodge this, 3D printing is increasingly being utilized to make tweaked, patient-specific inserts with made strides usefulness.
For case, inserts can be outlined with moved forward porosity and surface surface, encouraging the growth of the tissue around the embed. This level of complexity can as it were be accomplished with 3D printing. SmarTech Publishing predicts that more than 2 million implants will be 3D printed in metal by 2025.
Furthermore, metal 3D printing can be utilized to form hip and knee joint substitutions, cranial reconstruction implants and spinal inserts.
Lima Corporate
Italian restorative gadget producer Lima Corporate has been bringing additively made hip inserts to showcase for 10 a long time, utilizing Electron Pillar Dissolving (EBM) innovation.
The company created a innovation for 3D printing biocompatible titanium in cellular strong structures that take after common bone. Such structures are utilized to coat an embed, permitting it to be way better coordinates with human tissue.
The innovation is said to have made a difference nearly 100,000 patients, empowering superior embed execution and results.
Great inflexibility
Key Applications:
warm administration applications (e.g. micro-heat exchangers), electrical building, apparatus embeds
Maraging steel (Device steel)
High quality, hardness and pliability (can be furthermore warm treated to improve hardness and soundness)
Key Applications:
Tooling (centers and embeds of pass on casting and infusion shaping instruments), useful models
Headstrong metals (tantalum, niobium and tungsten)
Tall hardness
Warm and wear safe
Tall erosion resistance
Chemically inactive
Tall warm solidness
Tall biocompatibility
Moo poisonous quality (tantalum)
Key Applications:
This bunch of metals is important for high-stress applications such as rocket and rocket thruster spouts, valves and manifolds; inserts (tantalum)
Valuable metals (gold, silver, platinum)
Bendable
Conductive
Generally simple to post-process (e.g. to machine, finish, and clean)
Challenging to 3D print straightforwardly. Regularly processed only with DMLS/SLM
Key applications:
Valuable metals are utilized for specialty applications such as embellishments (gems and observes), dental (crowns, trims and onlays)
How Is Metal Powder Used for Metal 3D Printing Technology?
A wide assortment of metal powders are built up into wrapped up components, employing a run of application/fusion methods and machines. The powder forms all work within the same way. Broadly talking, the fabric is put into the build plate and melded to adjacent particles, dynamically building up a wrapped up portion.
Outline Of Metal 3D Printing Technology
This article surveyed four of the 3D printing innovations that are utilized for making metal parts and items. To memorize more approximately the sorts of Metal 3D Printing Technology for metals and in the event that it is the correct innovation for your application, contact a Xometry Agent.
Xometry gives a wide range of fabricating capabilities, counting Metal 3D Printing Technology and value-added services for all of your prototyping and generation needs. Visit our website to memorize more or to ask a free, no-obligation cite.
Copyright and Trademark Takes note
Inconel® may be a enlisted trademark of Huntington Amalgams division of Uncommon Metals Corp., Huntington, WV.
Hastelloy® s a registered trademark of Haynes Worldwide, Kokomo, Indiana.
Disclaimer
The substance showing up on this webpage is for educational purposes as it were. Xometry makes no representation or guarantee of any kind, be it communicated or inferred, as to the exactness, completeness, or legitimacy of the data. Any execution parameters, geometric resiliences, particular plan highlights, quality and sorts of materials, or forms ought to not be inferred to represent what will be conveyed by third-party providers or producers through Xometry’s network. Buyers looking for cites for parts are dependable for characterizing the particular prerequisites for those parts. If it’s not too much trouble allude to our terms and conditions for more data.
Benefits of Metal 3D Printing Innovation for the Honda Dashing Group
There are a few benefits of utilizing Metal 3D Printing Technology for the Honda Racing Team. To begin with and preeminent, this innovation permits for the creation of custom parts that are custom-made to their particular needs. By using this innovation, the group can make parts that are optimized for execution, coming about in faster and more spry cruisers.
Another advantage of Metal 3D Printing Technology innovation is that it permits for quick prototyping. This implies that the group can rapidly make and test modern plans, without the require for costly tooling or generation runs. This gives them a significant advantage over their competitors, as they can rapidly emphasize and improve their plans.
Moreover, Metal 3D Printing Technology innovation is environmentally friendly. This innovation produces altogether less squander than conventional fabricating strategies, lessening the team’s carbon impression.
Challenges of Metal 3D Printing Technology for the Honda Dashing Group
While Metal 3D Printing Technology innovation has numerous benefits, it moreover presents several challenges for the Honda Dashing Group. One of the critical challenges is the tall fetched of the gear. Metal 3D printers can be costly, and the fetched of the crude materials can too be tall. Furthermore, the method of making metal parts through 3D printing can be time-consuming, which can impact the team’s generation plan.
Another challenge is the require for specialized skill. Metal 3D printing innovation is still relatively new, and there are not numerous specialists within the field. The Honda Racing Team has to discover people with the mastery to function and keep up the gear, as well as plan and create parts utilizing the innovation.
Future of Metal 3D Printing Innovation for the Honda Dashing Group
In spite of the challenges, the Honda Dashing Team is committed to utilizing metal 3D printing innovation for their cruisers. They see this innovation as a way to thrust the boundaries of what is possible in motorsports. As the innovation proceeds to make strides and gotten to be more reasonable, it is likely that we’ll see increasingly teams adopting this innovation.
Within the future, we may see Honda Dashing Group utilizing metal 3D printing innovation to form not only custom parts but also entire cruisers. This might revolutionize the world of motorsports, because it would permit groups to form totally one of a kind and optimized bikes for their riders. Furthermore, as the innovation progresses, we may see Metal 3D Printing Technology gotten to be more reasonable, making it more open to smaller teams and autonomous riders.
Another exciting improvement is the potential for on-demand printing. This implies that the Honda Racing Group may possibly print parts on-site at a race occasion, permitting for quick repairs and alterations. This might be a significant advantage within the fast-paced world of motorsports, where each moment checks.
In general, long run of Metal 3D Printing Technology for the Honda Hustling Group is shinning. As the innovation proceeds to move forward and become more accessible, we may see this innovation gotten to be the standard in the world of motorsports. With the Honda Dashing Group driving the way, we can expect to see energizing advancements within the world of bike dashing.
Conclusion
The Honda Racing Team is at the forefront of advancement within the world of motorsports, utilizing Metal 3D Printing Technology to make custom parts for their bikes. This innovation permits for the creation of complex shapes and plans, coming about in motorcycles that are both useful and tastefully satisfying. Whereas there are challenges to utilizing this innovation, such as the tall cost of equipment and the require for specialized expertise, the benefits exceed the drawbacks. As the innovation proceeds to progress, we can expect to see increasingly groups adopting this innovation. Long-standing time of metal 3D printing innovation for the Honda Dashing Group is shinning, and we can’t wait to see what they come up with next.
Facebook: https://www.facebook.com/Motobikeinworld
Twiter: https://twitter.com/motoinworld2023
Instagram: https://www.instagram.com/motoinworld/
Pinteres: https://www.pinterest.com/motoinworld/
Linkedin: www.linkedin.com/in/motoinworld